Product real map:
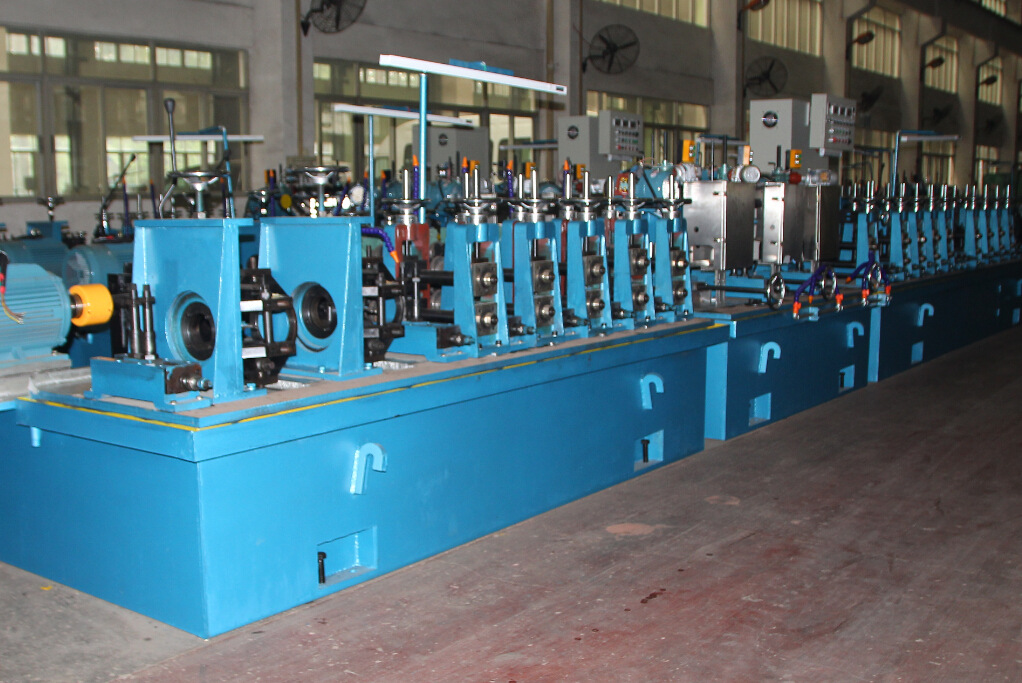
Product details
1. Stainless steel decorative pipe control machine
The
stainless steel decorative pipe machine is mainly used for the
production of stainless steel pipes and carbon steel pipes for
decoration, products, household appliances, etc. The products produced
by this series of moulds are round, square and rectangular pipes, as
well as elliptical, semi-circular and plum-blossom pipes. Such as:
stainless steel staircase handrails, burglar proof doors and windows,
electric heating pipes, housing leakage pipes, etc.
2, automated production process:
Through
the continuous forming process of uncoiling, feeding guidance, marking,
forming, welding, external weld grinding, shaping and sizing, sizing,
cutting (coil), jointing, etc., the structure is fine and the operation
is simple.
3. Product characteristics: the machine is
strong, durable, high precision, fully automated, simple to operate,
continuous production, high efficiency, less waste of materials, high
yield, low production cost.
4, technical parameters:
Model | (mm) | (mm) | (mm) | (mm) | Power | L*W(m) |
Basic specification for pipe making machine |
met-30 | 30 | 20 | Φ5-Φ25 | 0.25-0.8 | 5.5KW | 19.5*1.0m |
met-S40 | 40 | 25 | Φ6-Φ40 | 0.25-1.2 | 5.5KW | 20*1.0m |
met-40 | 40 | 25 | Φ9.5-Φ50.8 | 0.25-2.0 | 7.5KW | 21.5*1.1m |
met-40L | 40 | 25 | Φ12.7-Φ63.5 | 0.25-2.0 | 11KW | 21.5*1.1m |
met-50 | 50 | 30 | Φ25.4-Φ76.2 | 0.4-2.5 | 15KW | 24*1.2m |
met-60 | 60 | 40 | Φ50.8-Φ114 | 0.7-3.0 | 18.5KW | 26*1.4m |
met-80 | 80 | 50 | Φ76-Φ168 | 1.0-4.0 | 36.5KW | 32*2.3m |
met-100 | 100 | 70 | Φ114-Φ219 | 1.5-4.5 | 45KW | 36*2.5m |
Operational considerations:
1, ensure smooth production and meet product requirements.
1.2 effective maintenance of equipment.
1.3,
write reasonable operation instruction procedures to ensure the
production plan and product quality achieve the desired goals.
2, scope of use:
Workshop management department.
3, rules:
3.1 ensure the effective cleaning of equipment and record of cleanliness during shift.
3.2
accurately control the operation of the machine before shift and
coordinate with normal production. Pay attention to the opening of
water, gas or electricity, grinding the wheel, saw blade and cutting
table.
4, boot:
4 before starting, according to the
lubrication requirements, injecting different lubricants to the parts
where the lubricating oil is required to be injected.
4.1 first check whether the electrical switches are in the 0 position, then turn on the power supply.
4.2
Check whether the mechanical parts and pneumatic system are normal or
not. If there are abnormal phenomena, they should be checked and
eliminated in time so as not to cause mechanical equipment accidents.
4.3
Check the transmission gear is correct, otherwise there will be quality
problems, whether the pressure gauge of the cutting machine reaches
0.5-0.7 mpa, otherwise it can not be cut.
4.4 Let the motor run
empty for 2-3 minutes before going to work every morning. The
transmission gears are equal to 0. When driving, the operator is not
allowed to leave the machine tool and do other irrelevant things.
4.5
it is strictly prohibited to wear gloves to boot, long sleeved clothes
must wear hand sleeves, and long hair must wear a hat.
4.6 do not wipe the rotating parts when starting.
4.7 correctly adjust the mold, not vigorously under pressure, in place.
4.8
during the operation, you are not allowed to leave the machine tool.
You are not allowed to do other irrelevant things, and pay attention to
whether the welds are normal.
4.9 In the process of pipe-making,
the cutting strip must be consented by the workshop director, stored in
the belt-laying area, and recorded in detail with the sling operator on
the Production Process Card. It must not be discarded at will.
4.10
If abnormal phenomena are found in operation, such as smoke, burning
odor, sudden fuse burning, sudden extinguishment of indicator lights and
timely switching off the power switch to be checked out, then turn on
operation after troubleshooting.
4.11 the product's length is
checked regularly, not more than 6.01 meters, not less than 6 meters.
Strictly controlled between 4mm. The pipe on the unloading pipe rack
should not exceed 95% of the total capacity, so that the flat mouth
personnel should be lifted in time, otherwise the operator will be
responsible for the damage.
5, downtime:
5.1 stop welding while closing the power supply.
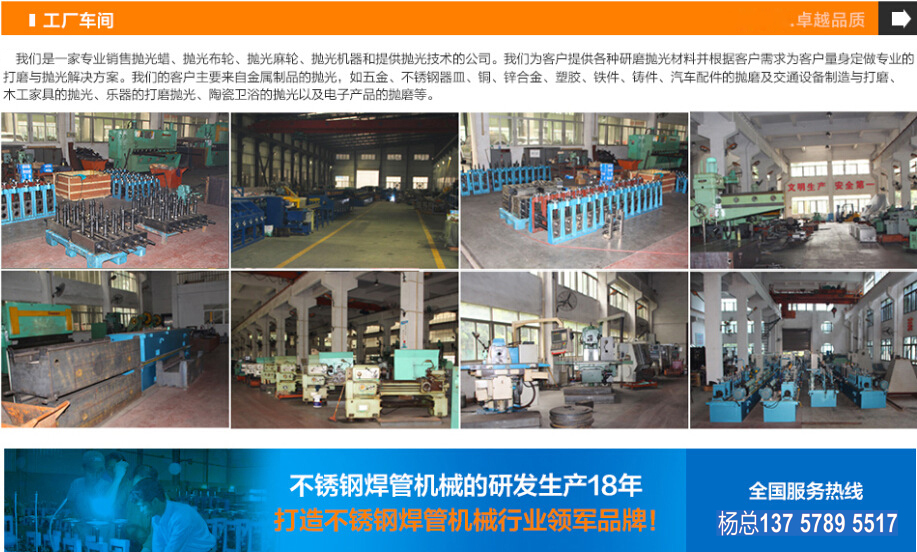
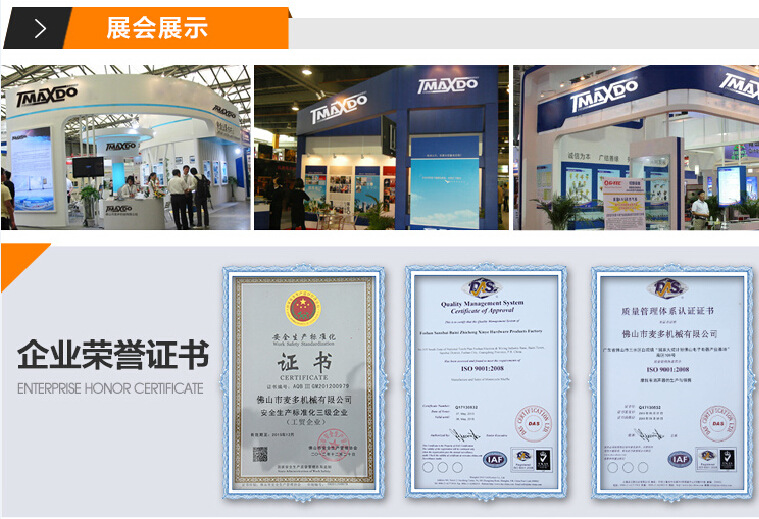
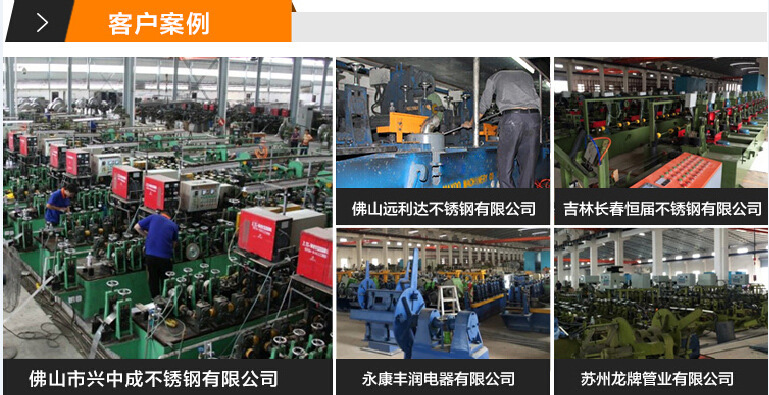
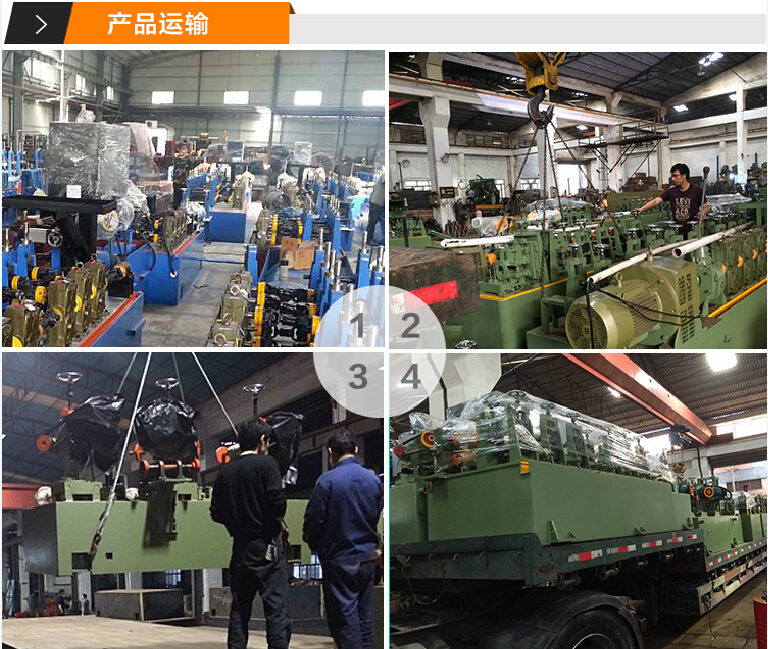